First radio implementation and history
Heinrich Hertz, 1887: First spark generator at Karlsruhe High-School for Technology
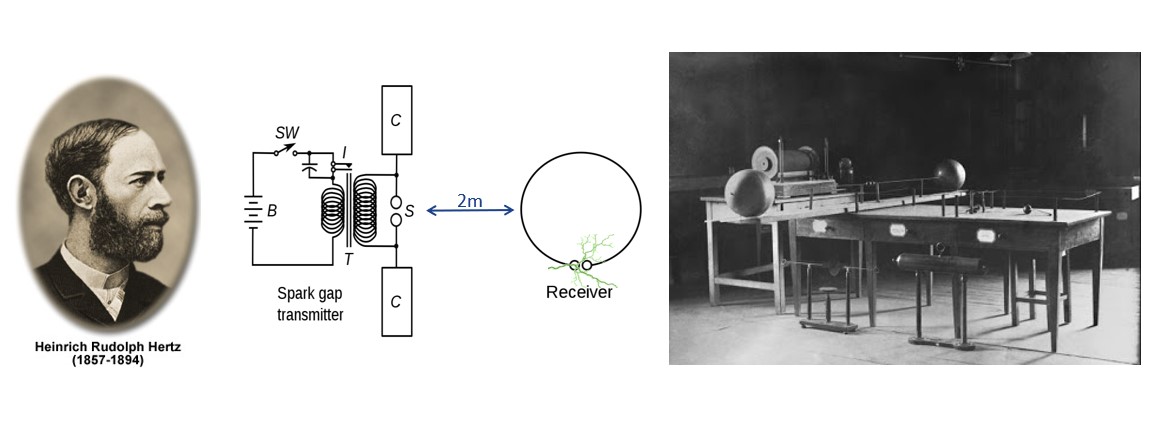
A century forward – base station technology in the digital age
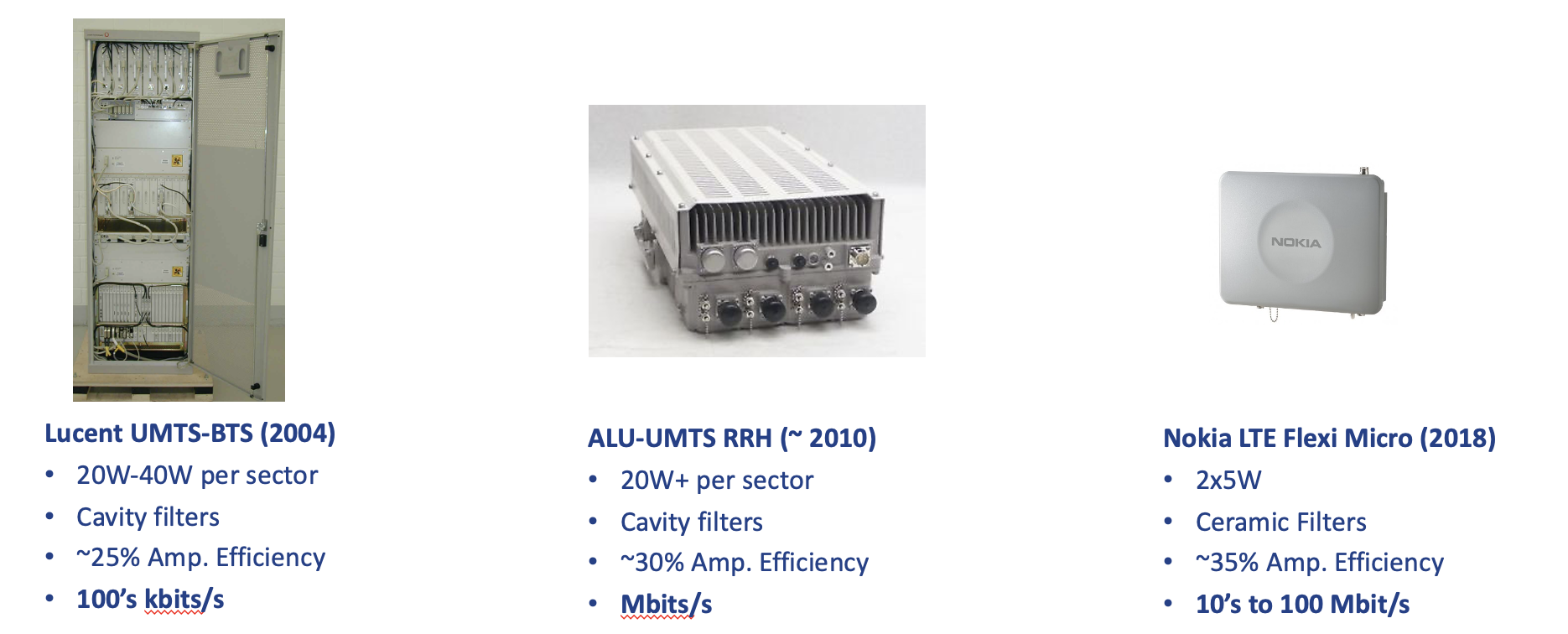
Motivation – Modern day
- Driven by size reduction – in base stations operating at lower GHz, size of diplexers over 70 % of the entire transceiver.
- Driven by cost – ceramic based filters have performance edge over cavity solutions, but it comes at cost.
- Driven by performance – assuming a base station with a power output of 50 dBm (100 W), losing 1 dB infers losing 20W.
- Frequency reconfigurability and tunability are becoming of greater importance as new bands are opening up, such as FR 2 (5G) and the likely need in 6G.
- Reconfigurability still in infancy, with great deal of effort dedicated to bulk-tuneable materials (Liquid Crystals, Ferro-electrics, Electro-chromic materials and Transition Metal Oxides)
Distributed Resonator – Basic Idea with two resonators
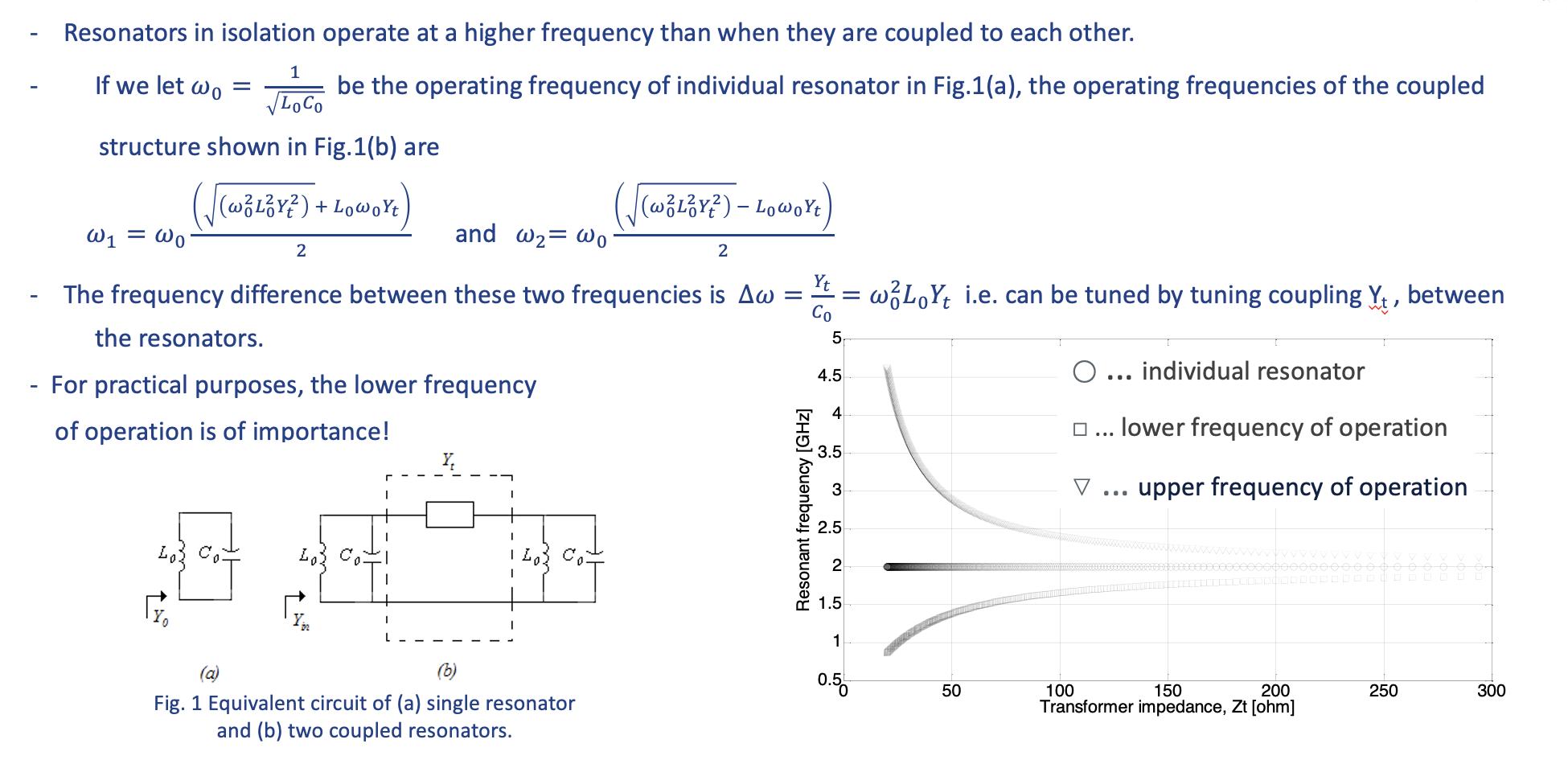
Distributed Resonator – with any number of individual resonators
Resonance distribution can be extended to a large number of individual elements for reduced frequency of operation.
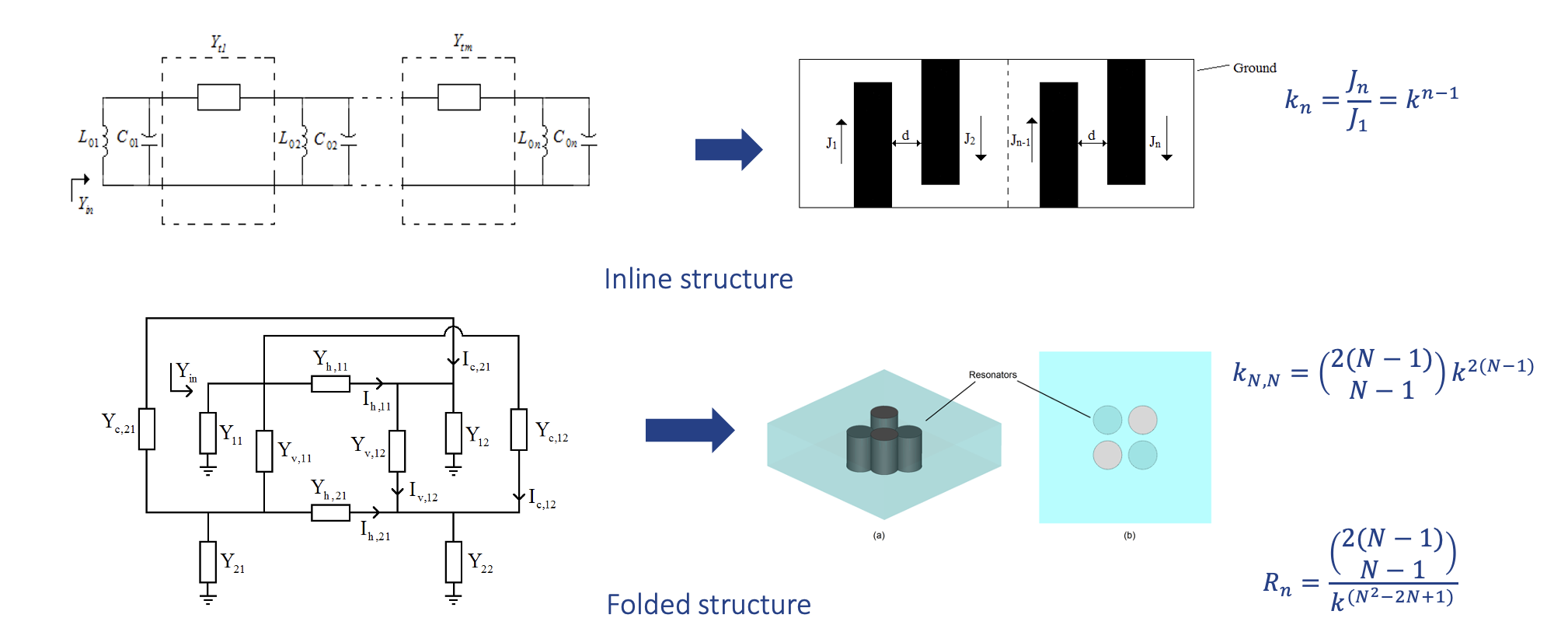
Distributed Resonator – Operation
Operating frequency can be reduced by folding individual resonant elements
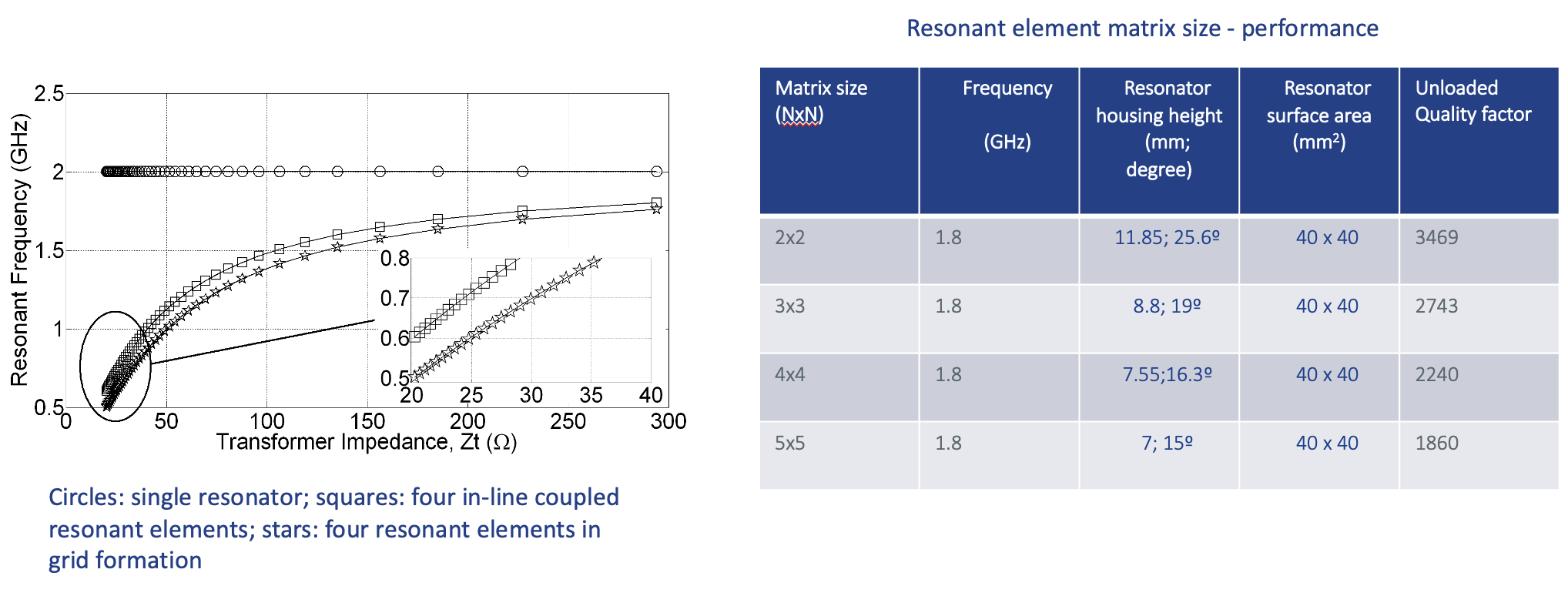
The frequency of operation of the folded structure is always lower than the inline structure
Distributed Resonator – 3-Pole filter Results
In order to test the theory, a 3-pole filter operating at 1800 MHz with a bandwidth of 40 MHz was designed and fabricated
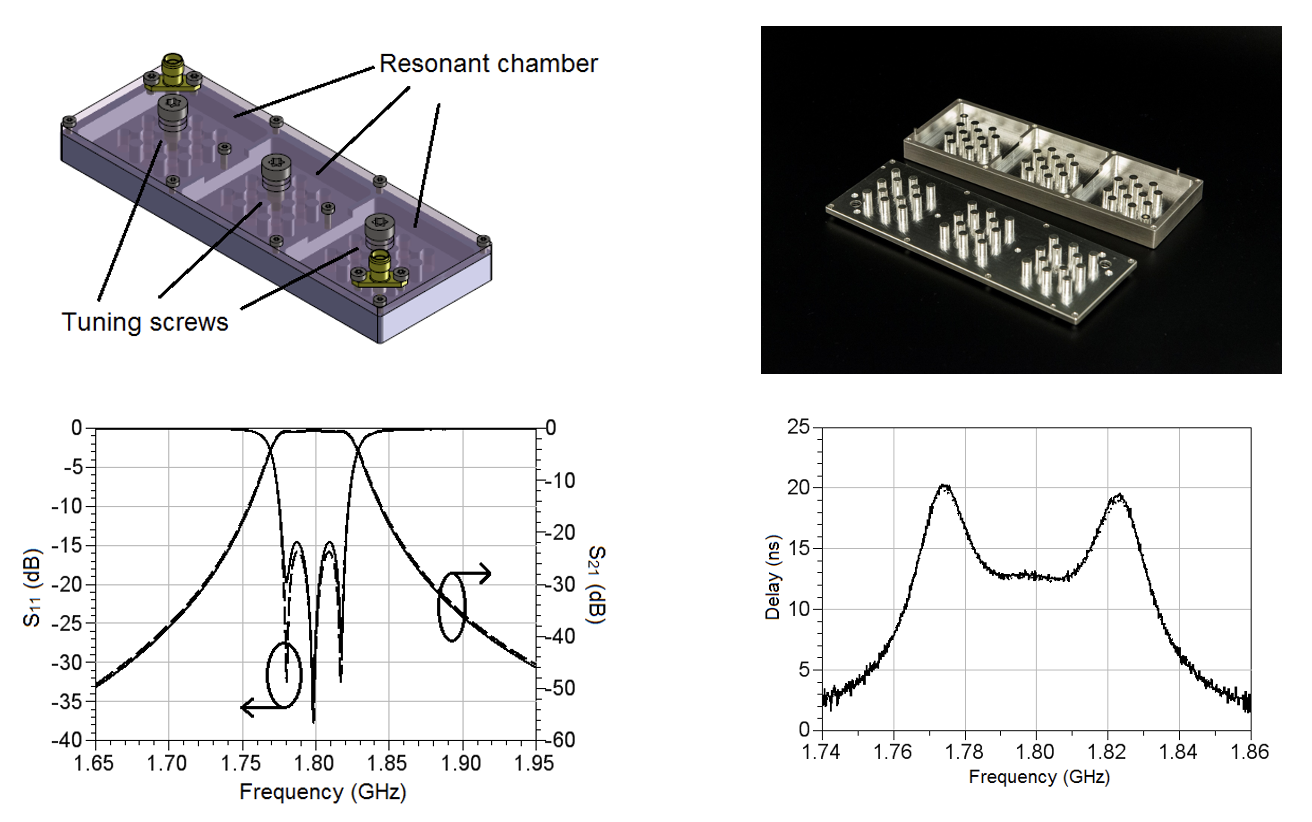
Each resonant chamber consists of 25 high frequency resonant elements – the tuning screw behaves as one of the resonant elements – unloaded Q of 1900.
Split-Distributed Resonator
-A more uniform distribution of electric field intensity among individual resonant elements should result in better electrical performance and better power handling
-Individual resonant elements are made in a distributed element fashion themselves
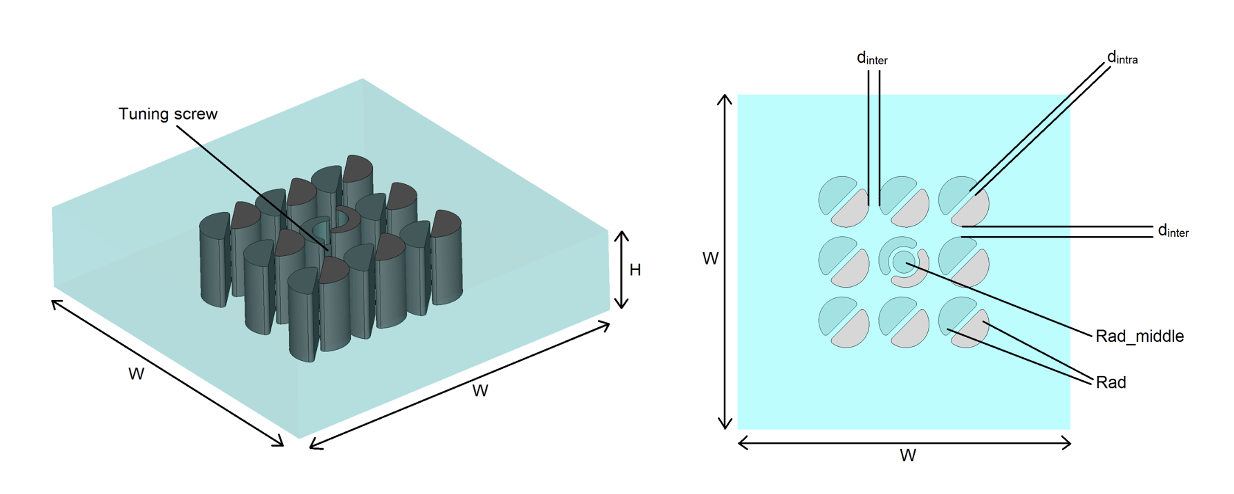
-Individual pairs couple among themselves (inter) and inside (intra) each other
-Coupling along the downward, left right diagonal of element pairs is achieved
-Resonant matrix can be arbitrarily extended
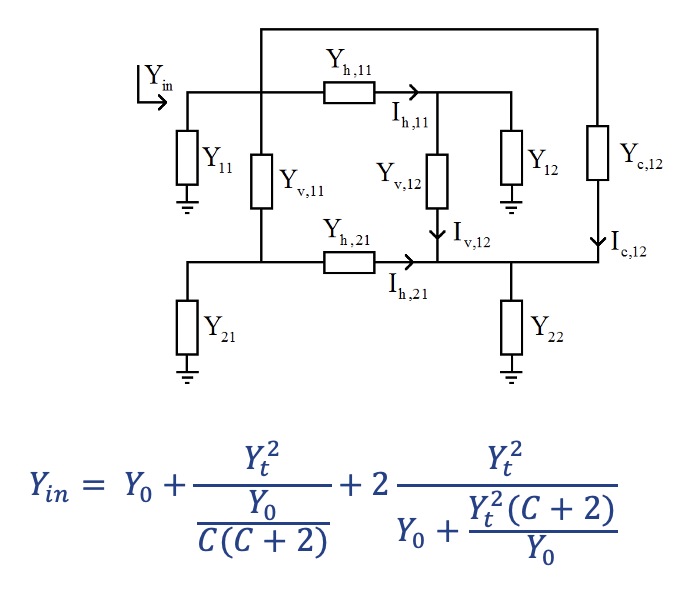
Split-Distributed Filter (5-pole)
-Each cylindrical element is split into 4 separate elements to obtain better distribution of electric field.
-Individual chamber size is 30 mm x 30 mm x 5 mm and consists of 3x3x4 (36) elements
-Maximum power handling of over 70 W (CW)
– Lower volume (over 40 % for same performance)
-Comparable power handling performance
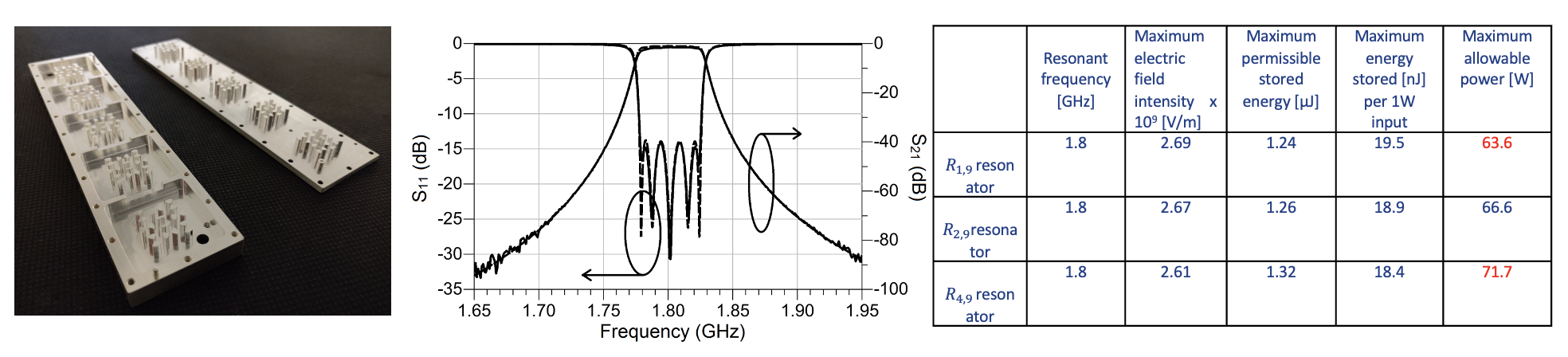
Varieties of distributed resonators – Co-centric distributed resonator and miniature coax-resonator
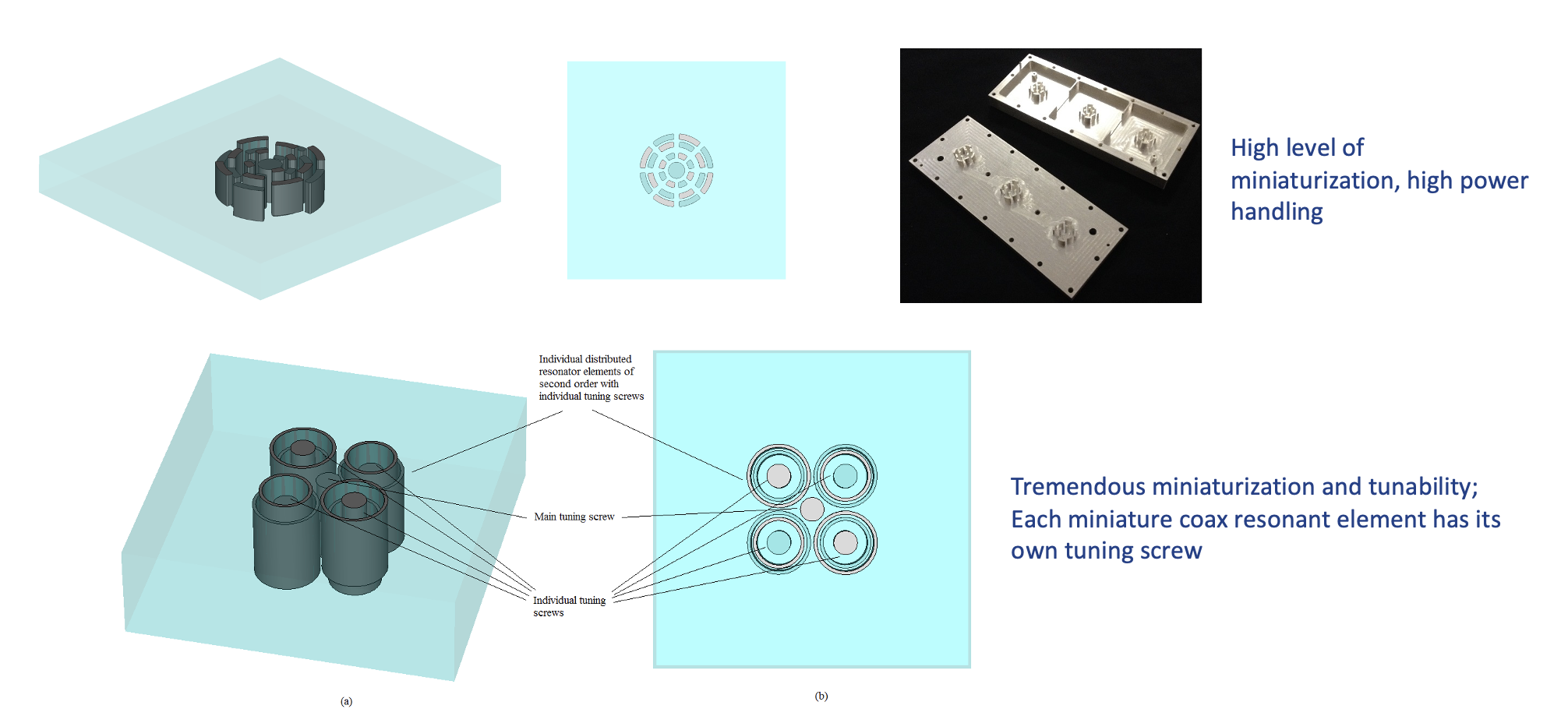
PCB Distributed Resonator – 3-pole Prototype I
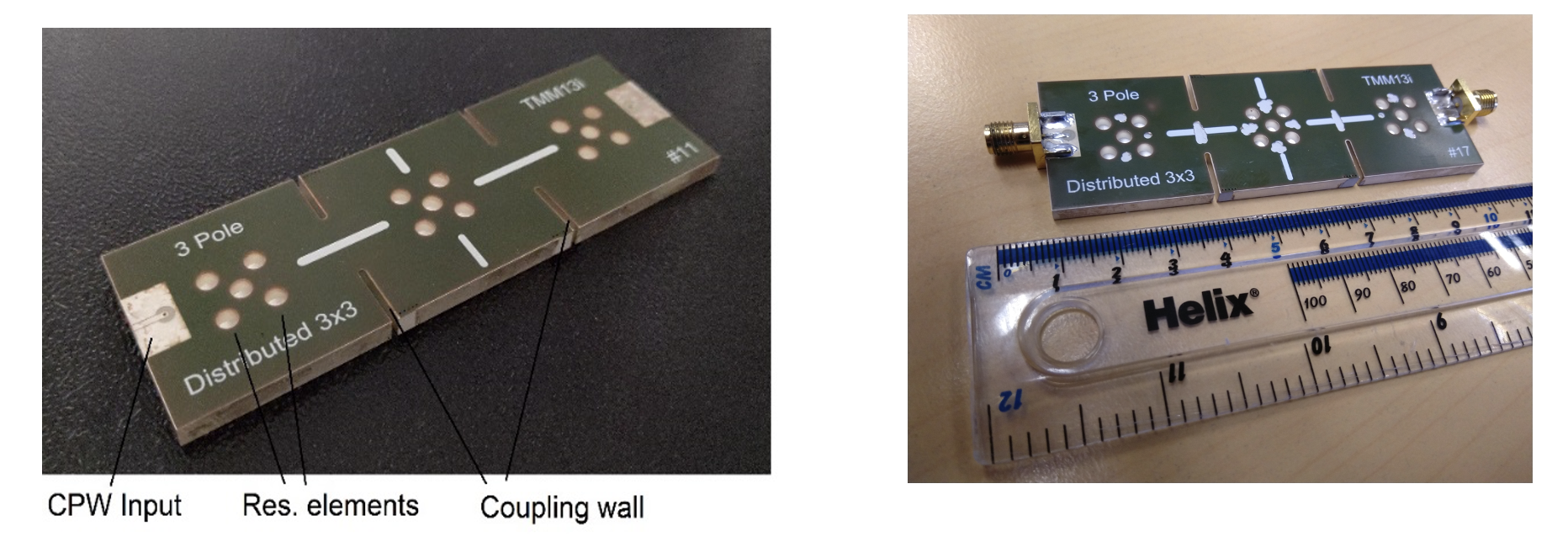
-3-pole filter fabricated using TMM 13 I substrate, with dielectric permittivity of 12.85
-Individual resonator dimensions are 30 x 30 x 3.175 mm3 , with unloaded Q of about 500
-Coupling walls achieved by subtractive manufacturing
Total filter dimensions 92 x 30 x 3.175 mm3
PCB Distributed Resonator – measured vs simulated results
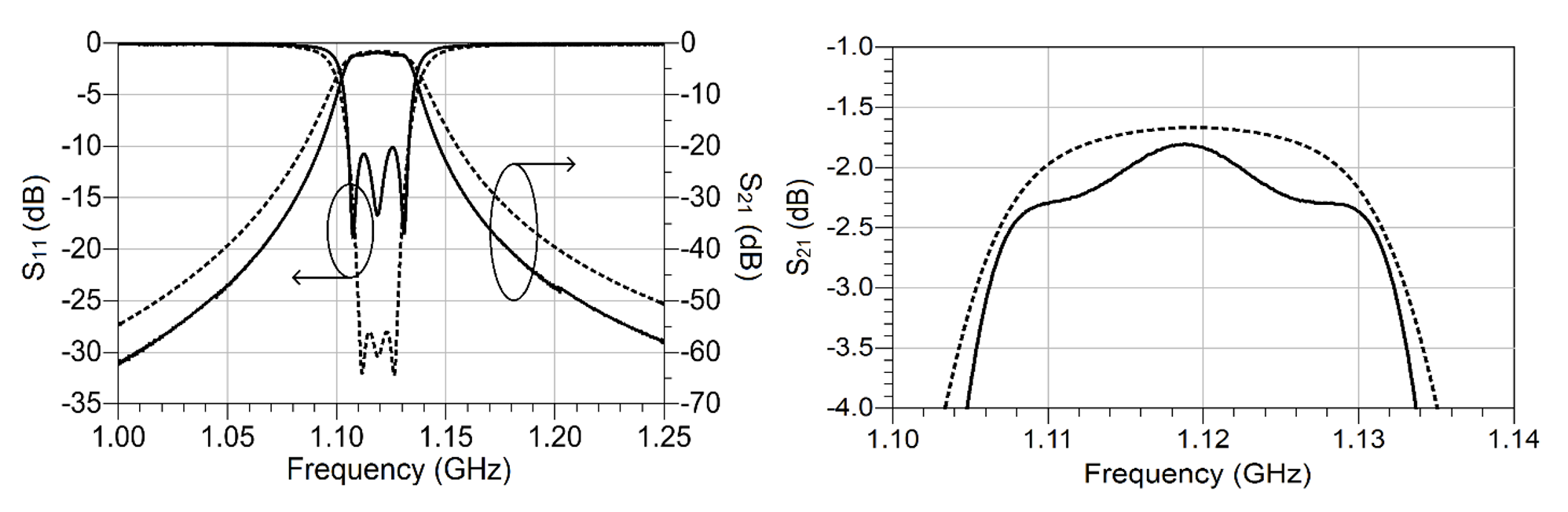
-Good agreement of tuned measured filter with simulations
-Predicted insertion loss of 1.67 dB vs measured insertion loss of 1.8 dB
-Predicted return loss is 16 dB while measurements show 10 dB in the corresponding frequency range
-Downside on the need for post-production tuning
11 x 11 Multilayered PCB Distributed Filter
-Eliminate the need for post-fabrication tuning – achievable by increasing the number of individual resonant elements. This eliminates the zero-mean statistical imperfections, such as drill depth. It does not eliminate deterministic errors (non-zero mean), such as different dielectric constants in measurements as compared to simulations
-Example below fabricated in PCB multi-layer technology consisting of 5 layer (Tachyon)
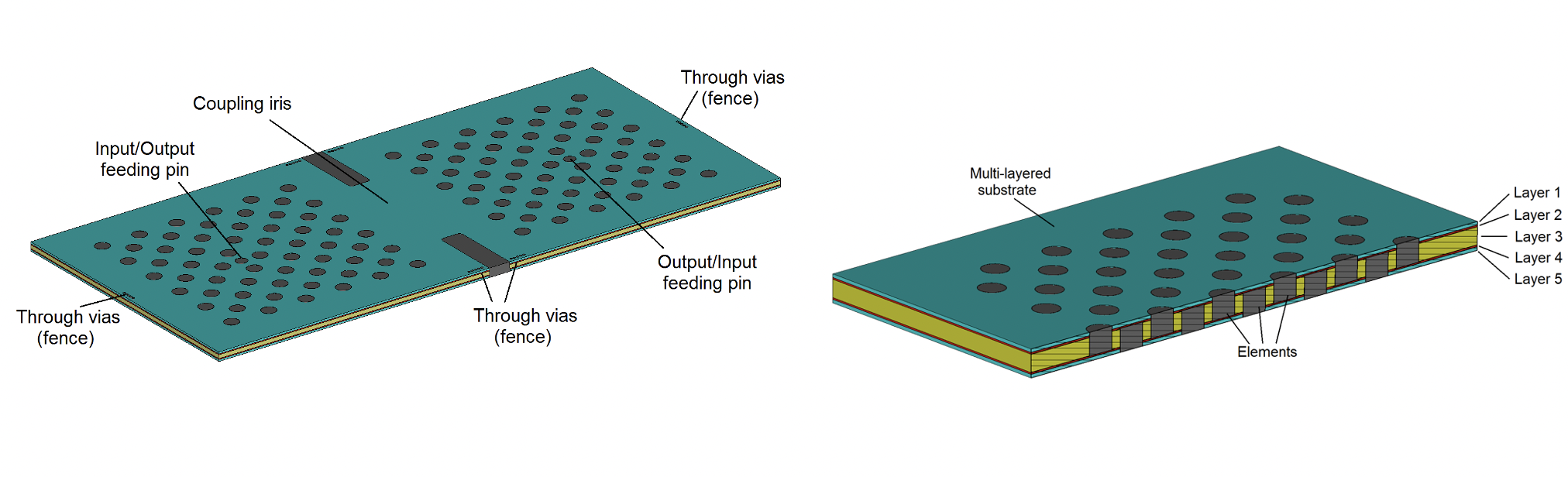
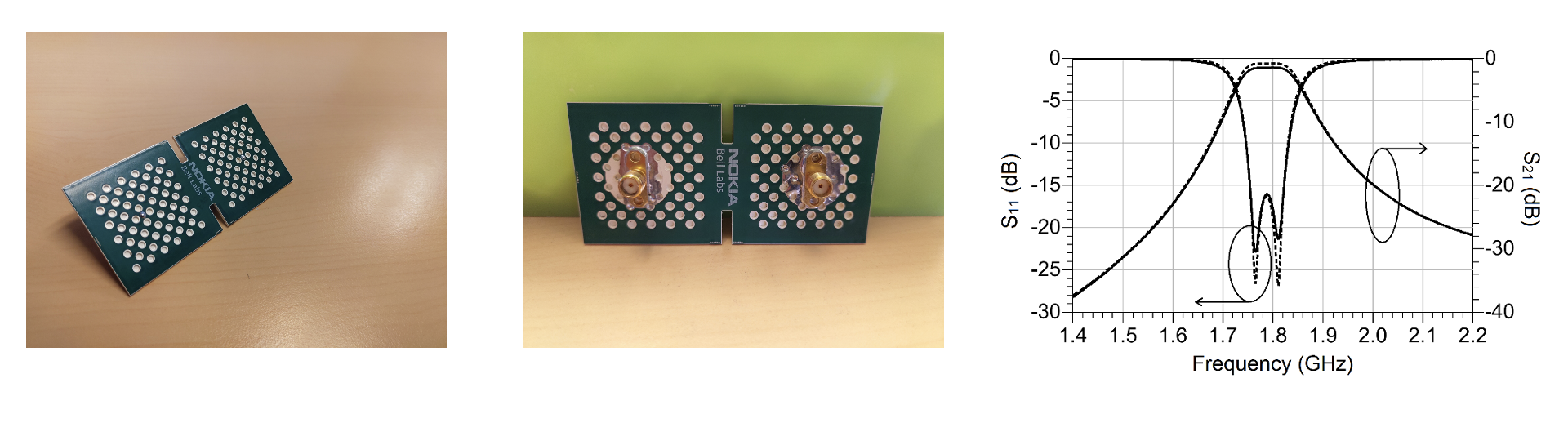
-2-pole filter fabricated using 5 Tachyon substrates pressed together, with dielectric permittivities ranging from 3.04 to 3.25
-Individual resonator dimensions are 40 x 40 x 1.27 mm3 , with unloaded Q of about 400
-Coupling walls achieved by subtractive manufacturing
-Total filter dimensions 82 x 40 x 1.27 mm3
-Very high power handling – no performance degradation even at 100 W (CW)
-No post production tuning
Metal drawn mm-wave distributed filter at 28 GHz (9×9 resonant element matrix)
Basic principle
- Use a large number of resonators
- Any variations in the manufacturing process is overcome by the collective properties of the design.
- Avoids postproduction tuning.
Characteristics
- Qu = 500, 6-pole filter (6 stacked resonant cavities in 2×3 configuration)
- Dimensions (each resonator): 5 x 5.5 x 0.4 mm3
- No need for post fabrication tuning using cost effective metal drawing
- Electrical height of only 13o
- Insertion loss of less than 1 dB only
Summary
1.Distributed resonators explained – trading height for surface area
2.Resonant frequency no longer a strong function of height
3.Very-low profile for given operational frequency – down to 100 while maintaining performance
4.Possibility of dimensional averaging – no post-production tuning required
Bulk Tuneable materials
To date:
- Liquid crystals (LC): nematic types examined, limited tuning range 20%-40%. Moderate bias voltages ~ 10 V (dc or low frequency ac). No memory effect.
- Ferroelectrics (FE): moderate to high bias voltages needed (depending on the thickness of films). High values of dielectric permittivities.
New materials:
- Dielectro-Phoresis (DP): movement of uncharged particles under the influence of gradient of electric field; slow. More research needed.
- Phase change materials: Creation of Magneli phases in the interior of oxides of certain transition metals. Moderate bias voltage (up to 10 V).
- Electro-Chromic (EC) materials: dielectric tunability discovered in 2016. Moderate bias voltages (~10 V dc), memory effect, easily tuneable absolute values of permittivity.
Dielectro-Phoresis
Facts:
- The movement of uncharged dielectric particles under the influence of non-uniform (gradient) of electric field.
- Commonly used in biological sciences to transport different particles.
- Different particles respond to different frequencies.
Research questions:
- Can dielectric characteristics be manipulated – can we induce dielectric tunability?
- Can we make RF devices based on DP?
- Can we improve on the speed?
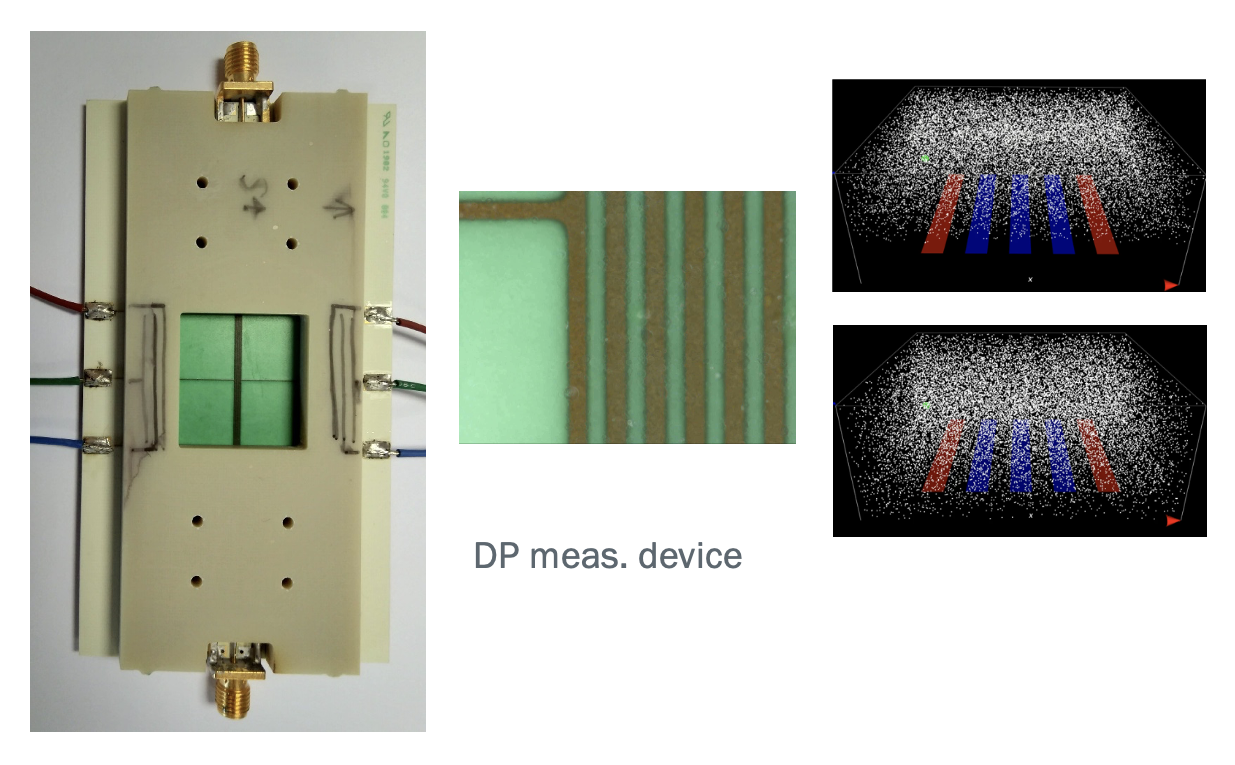
Phase Change Materials
- Phenomenon not fully understood, believed to be due to impurities in oxides of transition metals – formation of Magneli phases.
- Transition (Mott) from dielectric to metallic state induced by elevated temperature or application of DC bias.
- Most widely examined oxide VO2.
- Very promising research area.
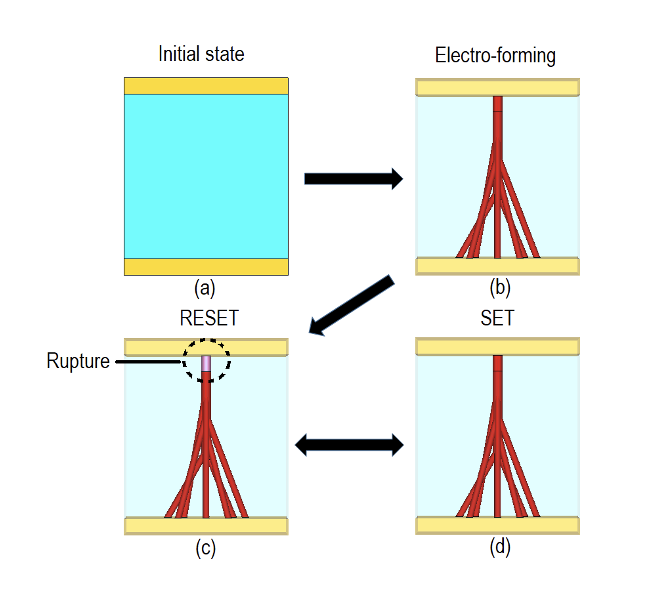
Electrochromism
- Electrochromism (traditionally) refers to changes in optical properties caused by movement of charges induced by external electric field
- Exhibited by several organic and inorganic compounds
- Electrochromic materials can revert to its original state by reversing electric field that produced the change
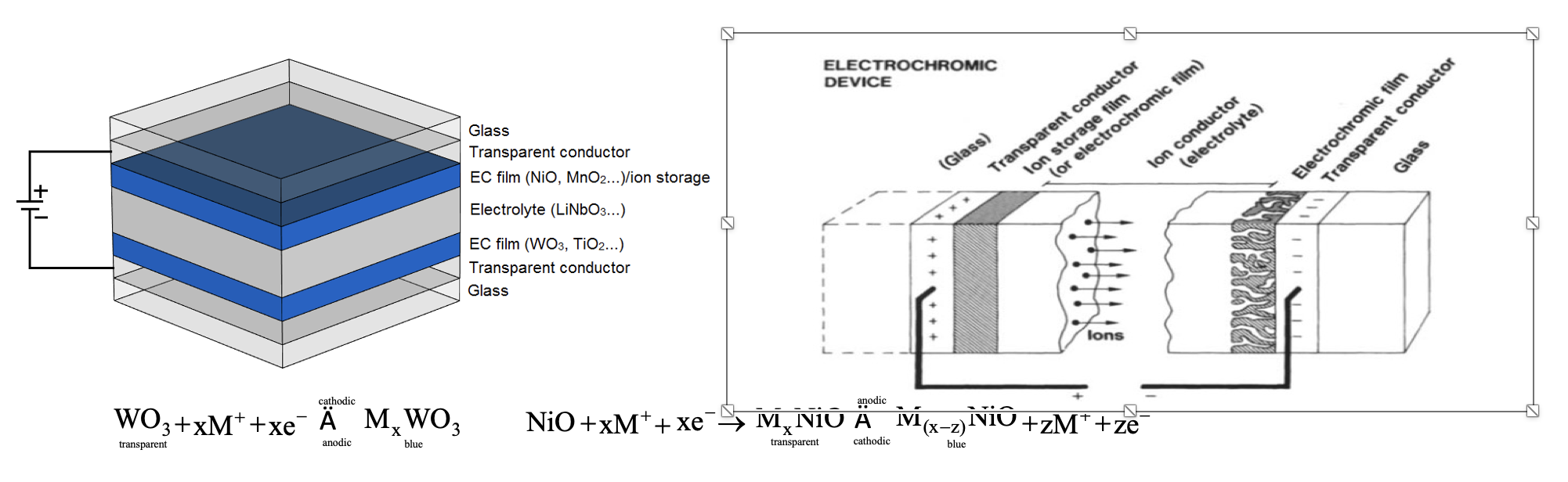
RF test measurement cell
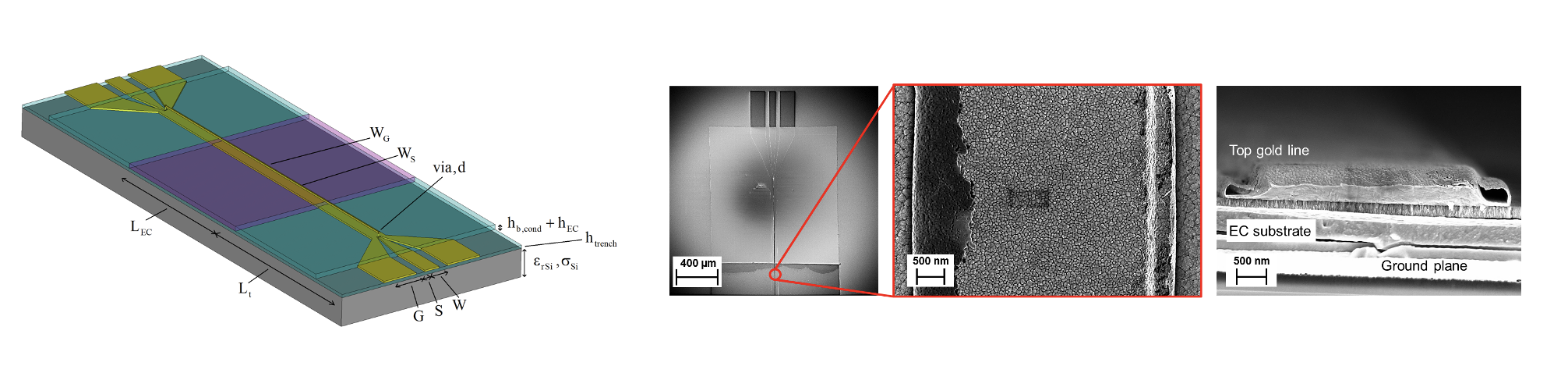
- Test well-known materials that exhibit optical EC effect for their RF potential (dielectric tunability).
- Inorganic materials are preferred due to their long life (NiO and WO3).
- Use height of LiNbO3 as parameter – two cases: 500 nm (cell 1) and 700 nm (cell 2)
Initial dielectric tunability results for 2 cells
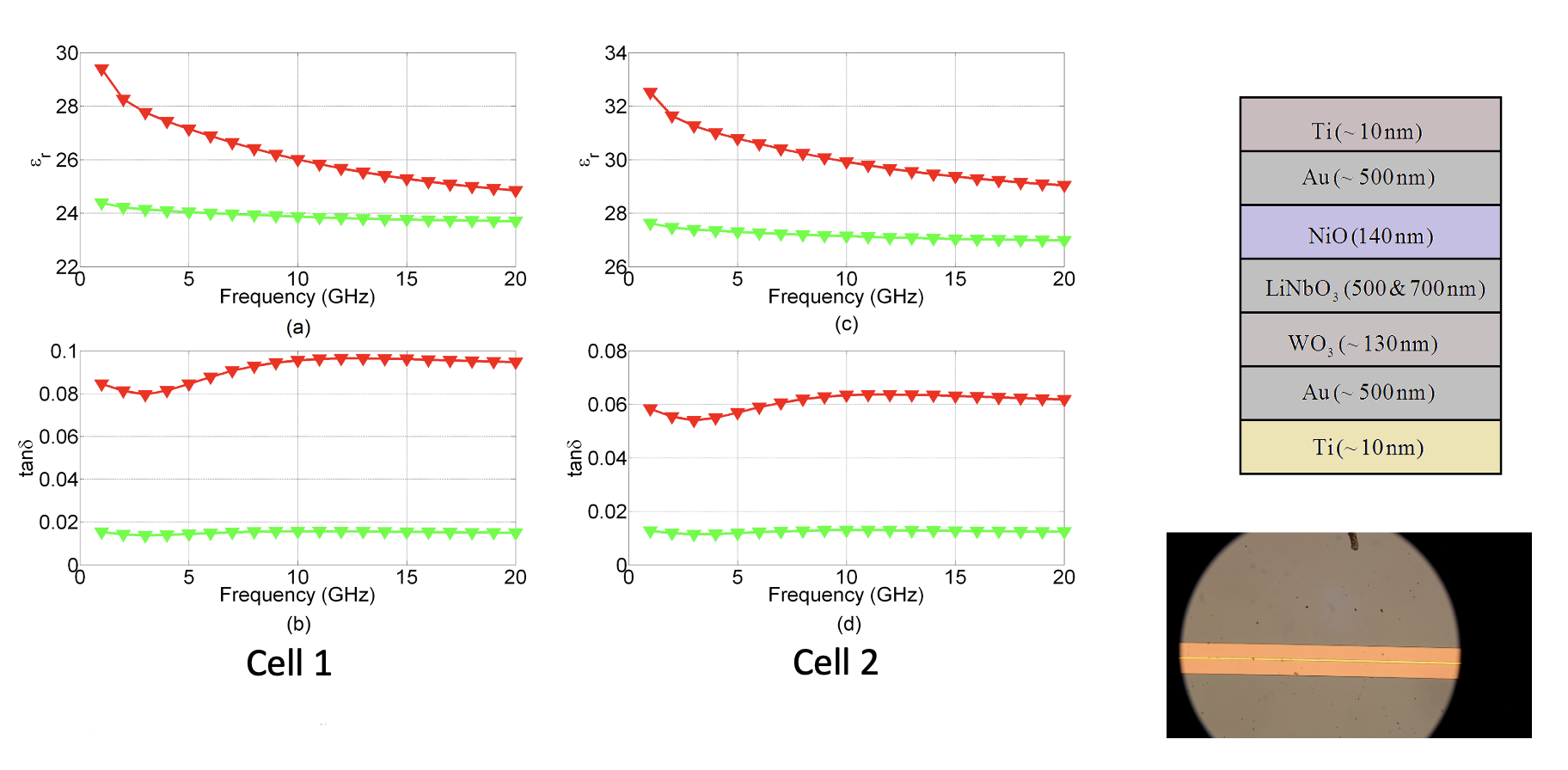
- Dielectric tunability of Cell 1 is between 5 % and 20 %, while for cell 2 it is between 8 % and 18 %
- Loss tangent tunability is much greater – it is over 360 % for both cells
Tuneable optical properties of EC
- Modulation of dielectric tunability at mm-wave frequencies extends to optical frequencies
- Can be modulated in a simple manner – by changing heights of LiNbO3 layer (500 nm and 700 nm)
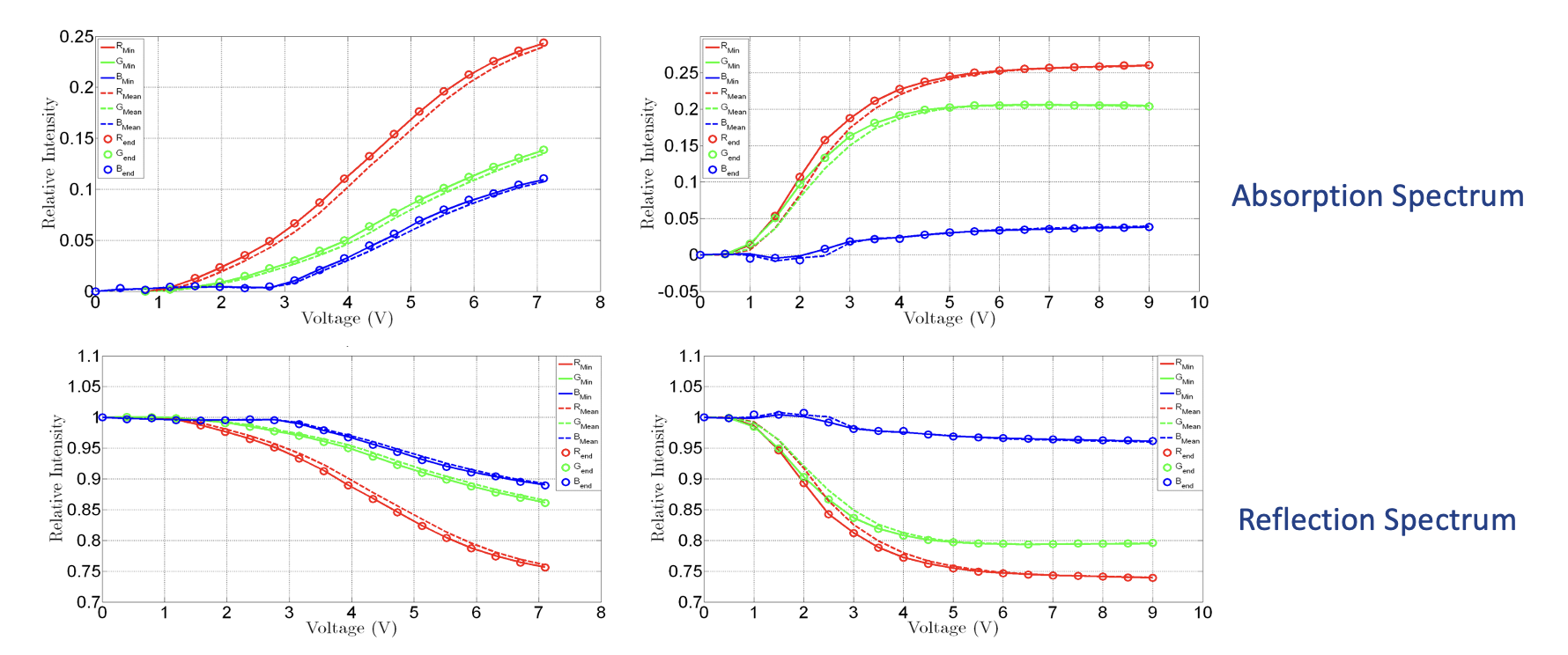
New EC cell structure – can we do better with standard NiO/LiNbO3/WO3 materials – LiNbO3/NiO/WO3/LiNbO3?
- Major limitation of standard EC cells lies with the fact that upon actuation, chromic layers become conductive, thereby reducing the channel height.
- A new EC cell structure shown below does not have such limitation
- Initial results indicate a change of no less than 80 % is achieved – tremendous result
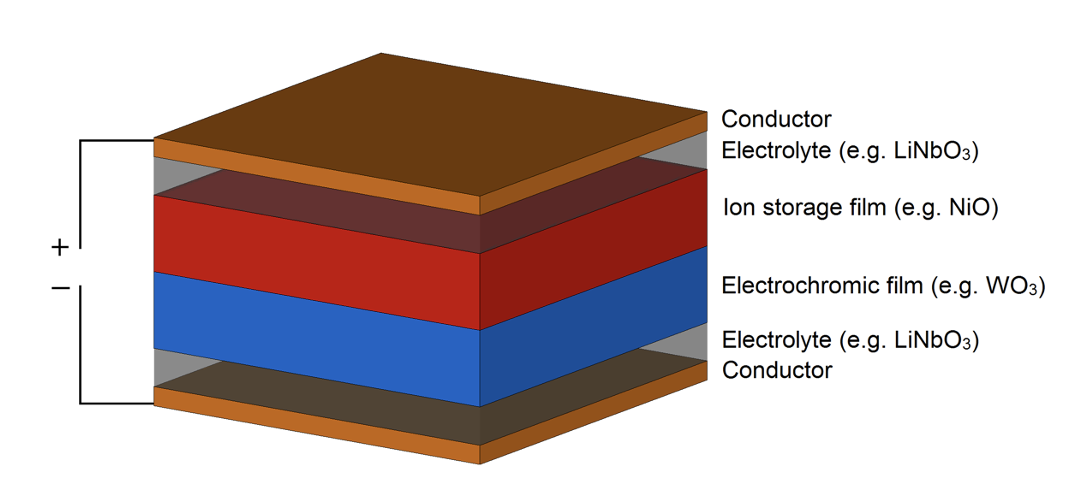
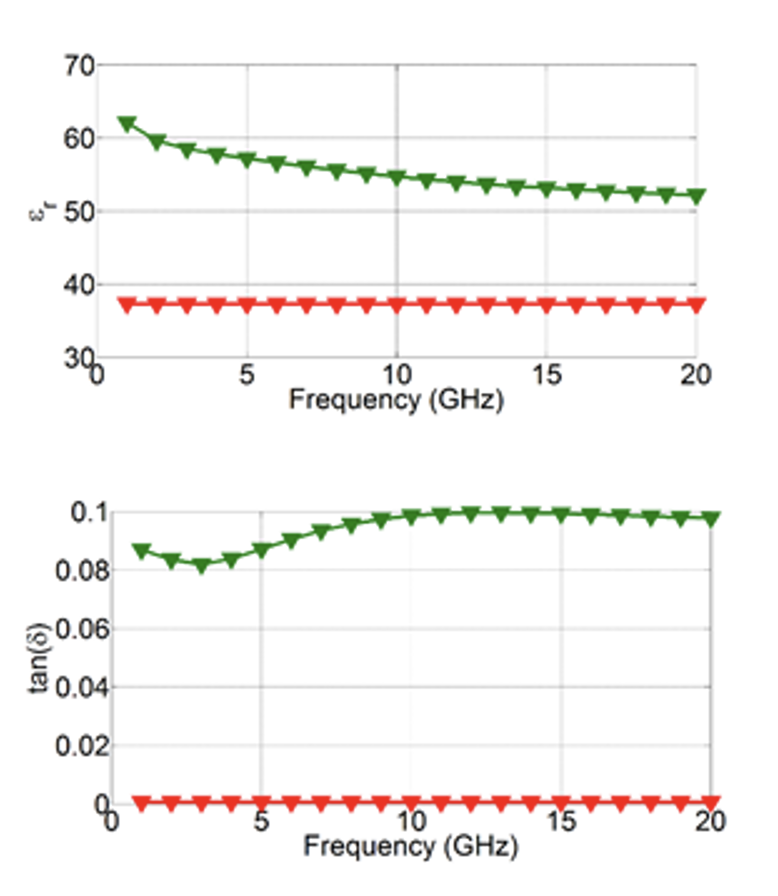
EC based Aperture-Coupled Reflectarray Element
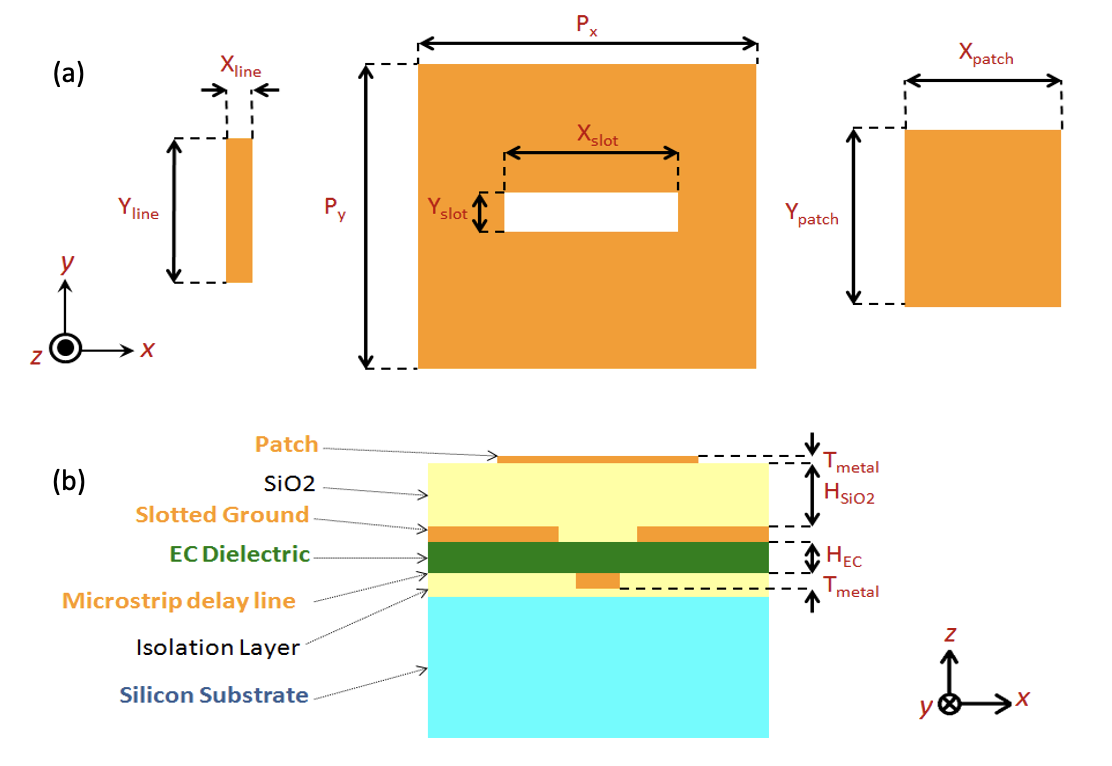
Topology of the EC- based aperture- coupled reflectarray unit cell (not to scale), [1] (a) front view and (b) side view. The delay line is etched in the isolation layer (SiO2 of thickness 2 µm), however, it is shown as a separate entity.
EC based Aperture-Coupled Reflectarray (5,000+ antenna elements)
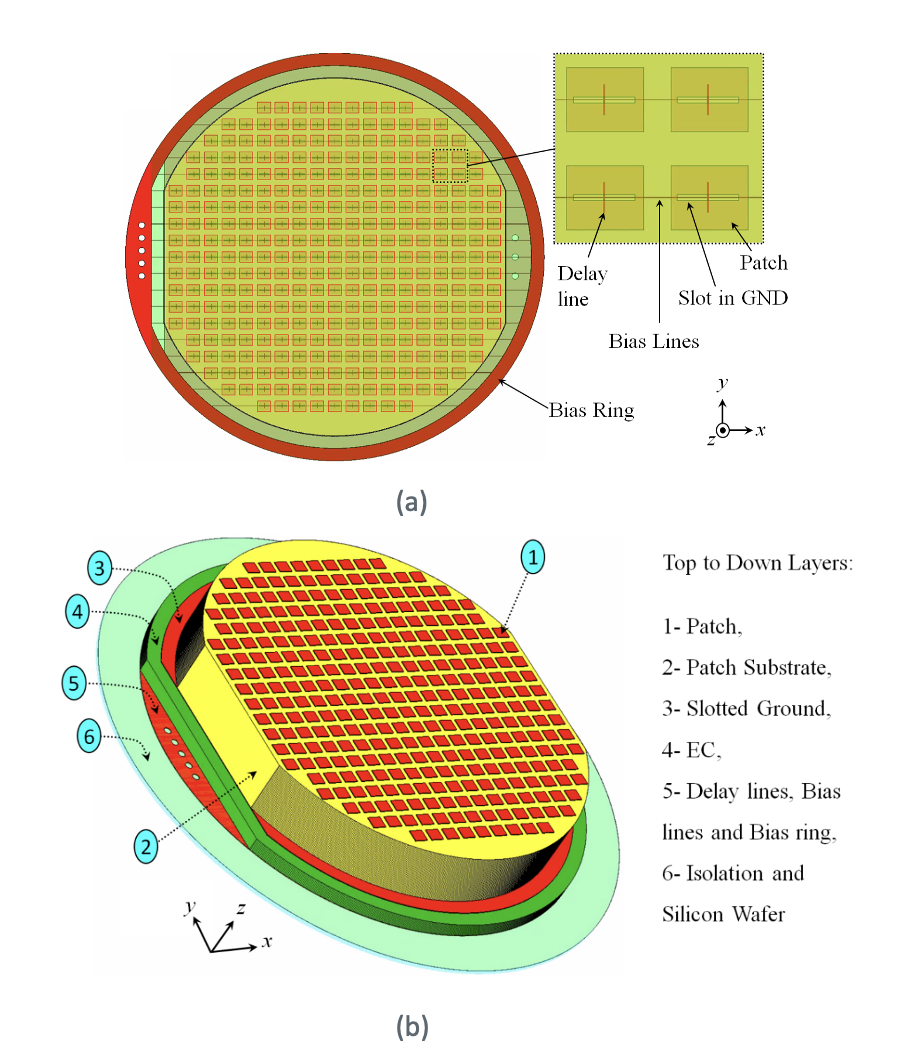
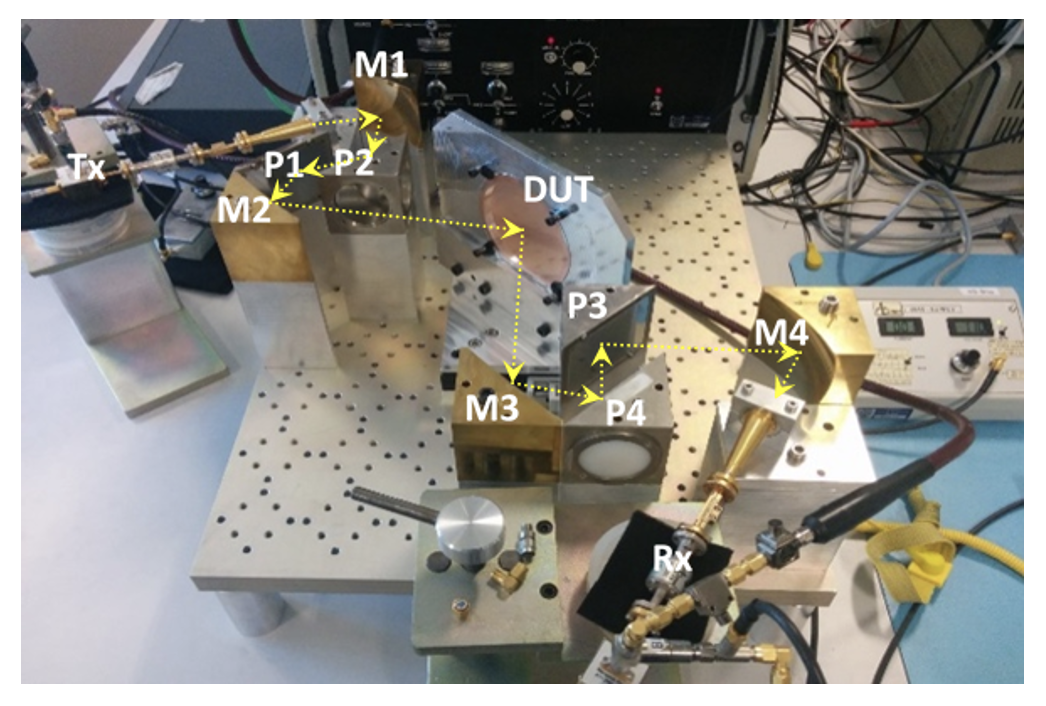
Test setup to be used for reflectarray measurements (M – mirrors, P – corner reflectors). The signal path is shown by yellow arrows.
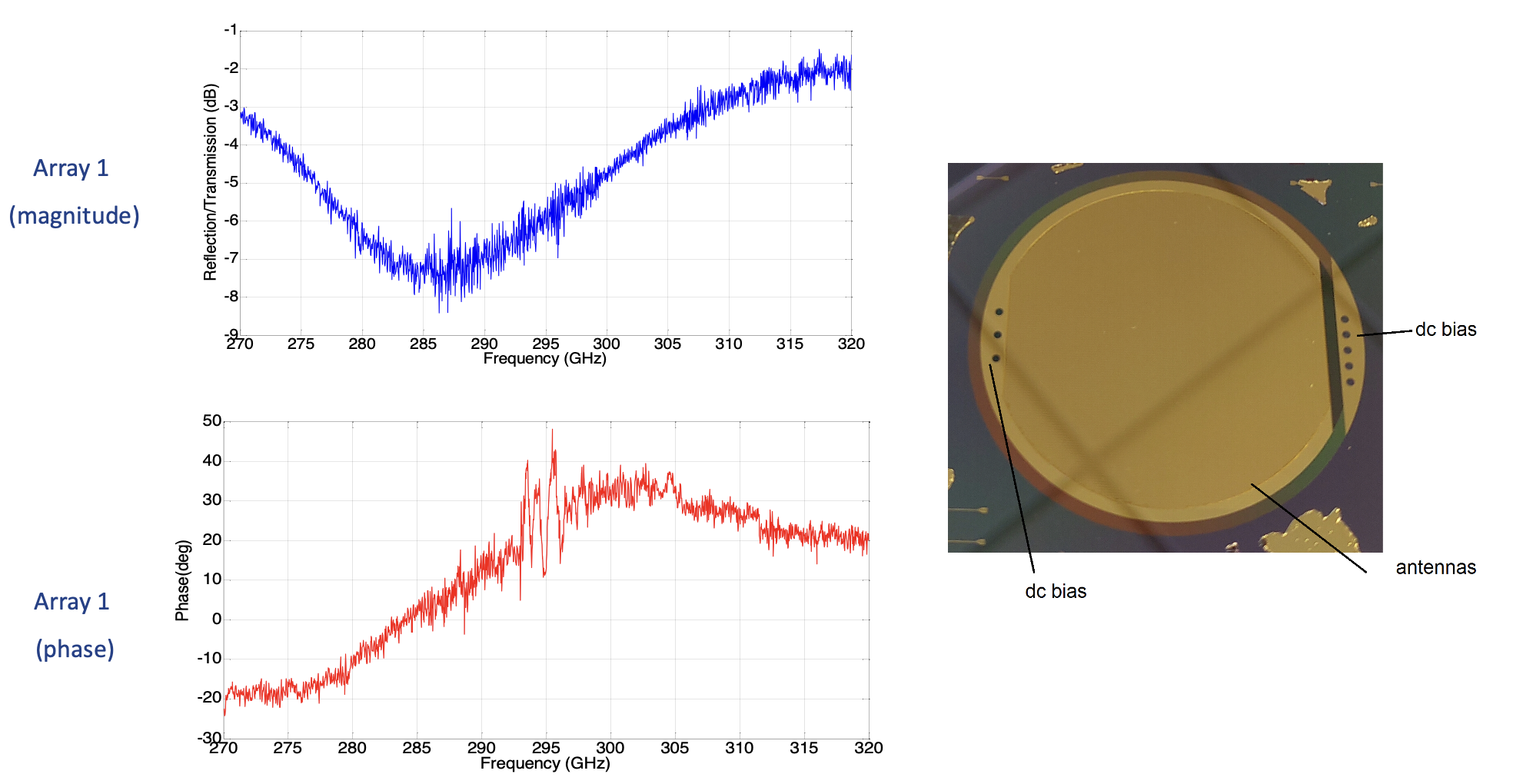
Summary
- Next generation technologies require high quality RF/mm-wave devices, filters among them.
- Flexible spectrum usage is expected to play a very important role.
- The focus is not only on new RF techniques, but the intricate interplay with new bulk tuneable materials.
- Several promising candidates are identified, but more work needs to be done.
- Fundamental challenges will need to be addressed by working closely with material scientists, chemists and engineers.
Leave a Reply